Medical
Shoe Moulds
3D printing technology is making steady progress in the shoemaking with its advantages of integrated forming, high efficiency, simple operation, safety and environmentally friendly, intelligent monitoring and management as well as automation. On basis of 3D digital manufacturing technology, Prismlab is committed to offering a comprehensive 3D printing solution for shoe moulds, creating user value and improving customer experience, building connections between "Mass Customization" and "Distributed Manufacturing" for shoe users, continuously integrates, creates and evolves brand-new business modes.
The low profit of single commodity is the characteristic of apparel products. The enterprise can survive in the case of mass sales with the help of low-cost supply and huge domestic and foreign market demand. However, with the rise of labor and raw material costs, the contraction of foreign trade market, corporate profits have been compressed to the limit or even appeared a loss. This also explains from another angle the importance of accelerating the new technology introduction and innovation.
Look abroad. Nike and Adidas have both started bringing 3D printing into production. Nike has unveiled “Vapor Laser Talon Boot” sneakers for American football players that use 3D printed soles to increase sprints. Adidas officials said the traditional shoe model would take 12 manual workers to complete in 4-6 weeks, while by virtue of 3D printing, it could be accomplished by only 2 workers within 1-2 days.
Application of 3D printing technology in footwear:
● To replace wood mould: utilizing 3D printing to directly produce shoe sample prototypes for foundry casting and precise printing to substitute for wood with shorter time, fewer labor power, less materials, more complex pattern selectivity of shoe mould, more flexible and efficient processing, lighter noise, less dust and corrosion pollution. Prismlab has applied this technology in mass production with good results.
● All-round printing: 3D printing technology can print the entire six-sides at one time, without any needs for knife path editing, knife changing, platform rotation and other extra operations. Each shoe mould is correspondingly customized to acquire accurate expression. Besides, the 3D printer can build multiple models with different data specifications at one time, which significantly improves the printing efficiency. Prismlab series of 3D printers use LCD light curing technology to achieve the most efficient mass production with an average printing period of 1.5 hours, which enables designers to evaluate the appearance and design of the sample and is suitable for the demonstration of marketing activities.
● Fitting sample proofing: during development of slippers, boots etc., fitting shoe samples shall be provided before formal production. 3D printing enables test the compatibility between the last, upper and sole along with directly print the fitting samples, greatly shortening the design cycle of shoes.
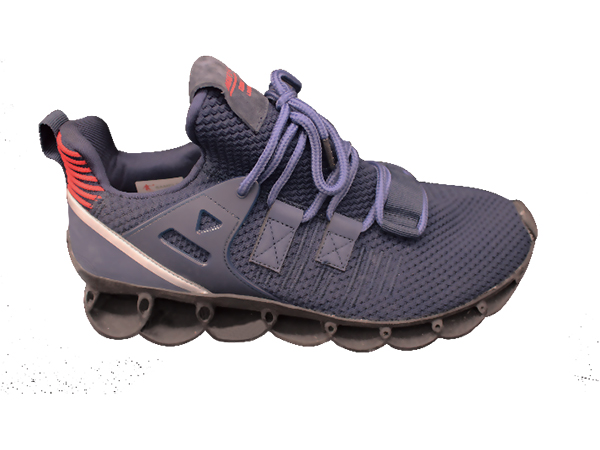
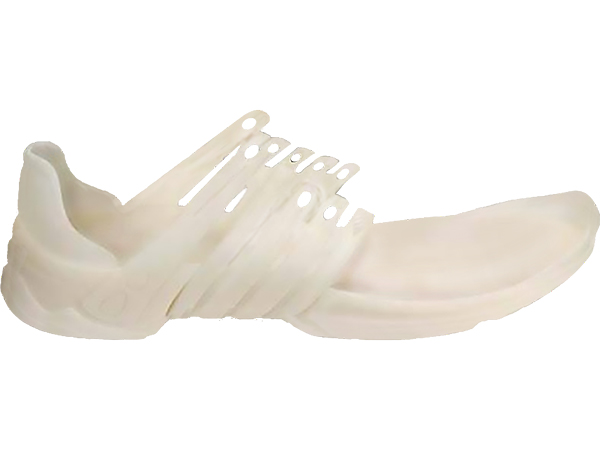
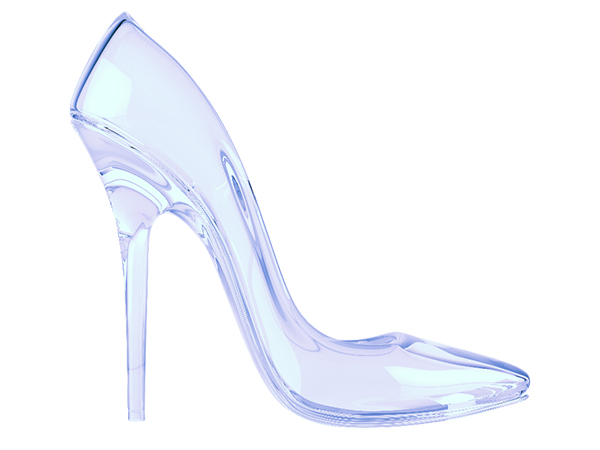
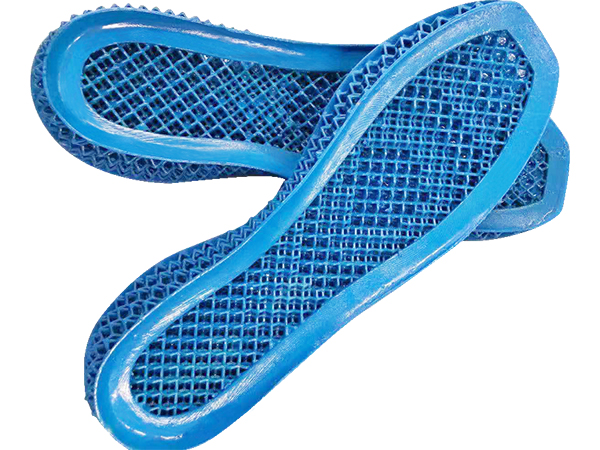